
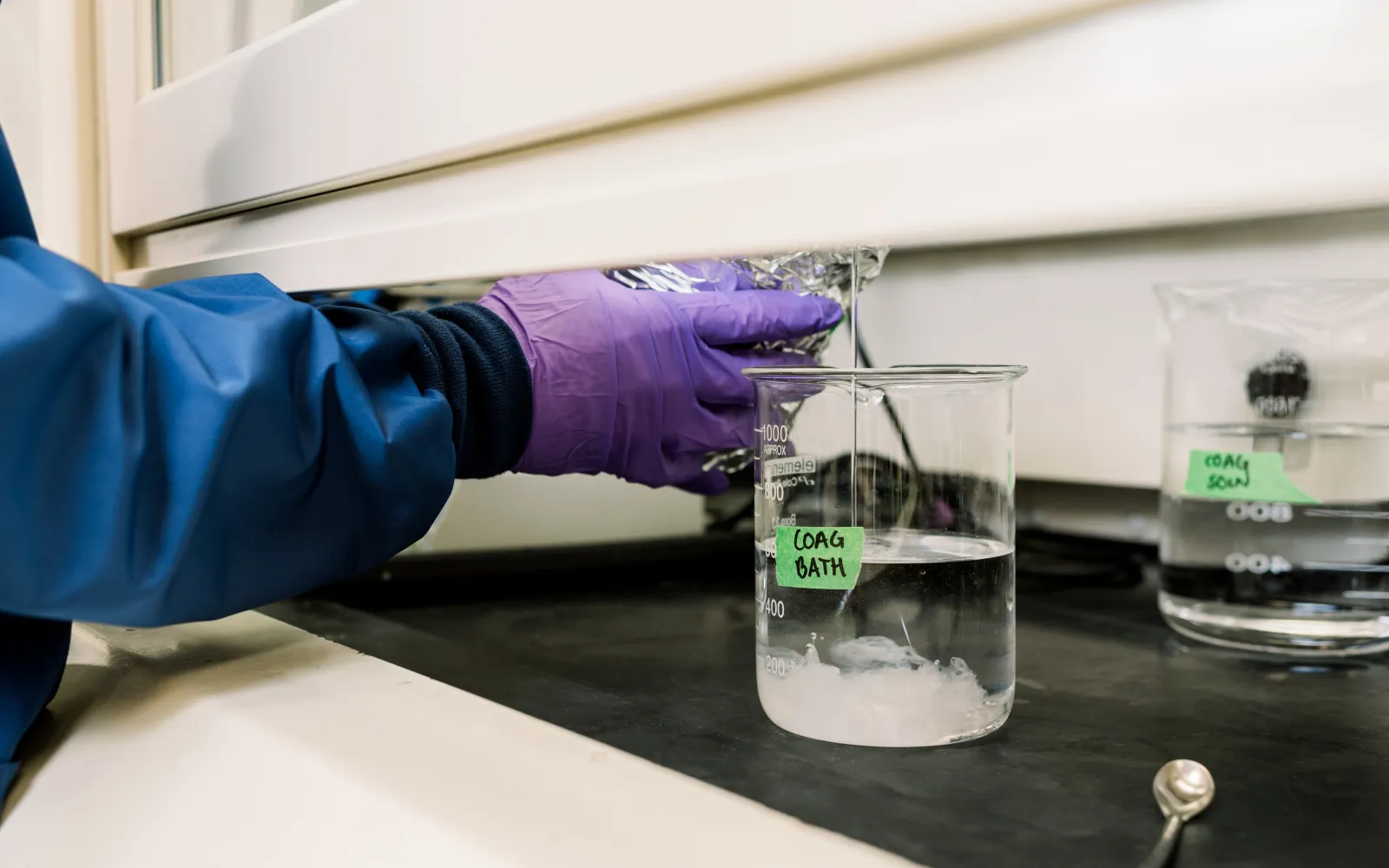
ZwitterCo
Membrane filters for the world’s toughest wastewaters
The world is getting hotter and, in many places, drier. Demand for water outstrips supply in much of the United States, including the Colorado River Basin, which is at its lowest level in 1,000 years. But Americans also waste a lot of water. Every day, industrial facilities in the U.S. discharge 255 billion gallons of wastewater into public waterways, most of which are treated through chemical, physical, or biological means. But it’s still not pure enough for industrial reuse. If it were, then facilities wouldn’t discharge it.
There are growing, urgent incentives to filter the contaminants out of industrial wastewater so that more can be recycled. But a problem wastewater industry insiders call membrane fouling has always stood in the way. Traditional water filters “foul” or clog up with particulates and organic debris so rapidly — requiring replacement or laborious cleaning — that they’re impractical or cost-prohibitive as a high-volume solution.
ZwitterCo, a DCVC-backed startup that spun out of the chemical engineering labs of Dr. Ayse Asatekin at Tufts University, has invented a technology that solves the problem of membrane fouling. The company, founded by Alex Rappaport, Christopher Drover, and Chris Roy, is commercializing a novel filter-membrane material with chemical properties that make it fouling-resistant, even in the face of extremely contaminated wastewater. ZwitterCo membranes exert such a strong pull on the water molecules in wastewater that, in effect, they’re sucked out, leaving behind only the waste particles, which can’t fit through the membrane’s pores.
That’s the breakthrough ZwitterCo licensed from Tufts and is now commercializing for use by food and beverage makers, livestock industries, and biologic drug manufacturers — industries where the captured waste can be as valuable as the recycled water. We know that reducing the demand on public water systems will be key to both industrial resilience and the nation’s food security. So here at DCVC we’re pleased to have led a $33 million Series A financing round for the company, announced on September 15, 2022.
“ZwitterCo” stands for zwitterionic copolymer, the type of material at the core of the company’s filters. In chemistry, an ion is any molecule with a net electrical charge, often created by functional groups or branches of atoms that stick out from the molecule’s main backbone. A zwitterion is a molecule that has an equal number of positively-charged and negatively-charged functional groups. (The prefix comes from the German word zwitter, for “hermaphrodite.”)
Even an organic polymer can be zwitterionic if it has the right functional groups. The important point for wastewater engineers is that while zwitterions are just as “hydrophilic,” or highly attracted to water molecules, as are highly soluble materials like salt, the zwitterionic copolymers that form ZwitterCo’s membranes have been engineered into highly functional plastics that maintain these water-loving properties. (Molecules of H2O are polar, with a slight positive charge on the hydrogen side and a slight negative charge on the oxygen side. A polar water molecule and a net-neutrally charged zwitterion experience an attraction that’s actually stronger than the weak ionic attraction between one zwitterion and its neighbors.)
Zwitterions are among the most hydrophilic of all organic molecules. Asatekin’s insight was to see that these extremely hydrophilic materials would serve as fouling-resistant filter membranes. In effect, hydrophilic surfaces grab water molecules and repel organic compounds such as fats, greases, oils, or proteins. The water in a wastewater stream forms a boundary sheet over the membrane, never allowing anything else to make long-term contact.
A membrane that’s so slippery nothing can accumulate on its surface solves half of the fouling problem. Unfortunately, membranes aren’t just a flat surface — they form a three-dimensional matrix. When they fail, it’s not usually because of surface accumulation, but because of pore fouling, when particles get stuck in difficult-to-clean corners of the pore channels. So Asatekin also came up with a self-assembling architecture with random continuous channels that extend all the way through the membrane. The channels act like the flumes at a waterpark, ushering through H2O molecules, while larger molecules stop at the surface. Cleaning a ZwitterCo membrane is simple: operators rinse off particles with water or use mild cleaning chemicals in particularly severe cases.
ZwitterCo spent its first two years, from 2018 to 2020, creating an efficient, roll-to-roll method for manufacturing Asatekin’s matrix; assembling the membranes into pressurized modules with ports for capturing both the permeate (clean water) and the concentrate (the waste product), and finding partners willing to field-test the technology. In 2021, ZwitterCo sold 16 commercial pilots. The first plant using ZwitterCo’s filters went online in late 2021 and has been running continuously ever since. The plant hasn’t had to clean its membranes in over six months of operation.
So far, ZwitterCo’s technology is being adopted most quickly in manure digestate treatment, meat and poultry treatment, dairy wastewater, and bioprocessing. In these businesses, the captured waste can be resold as feedstocks or fertilizer. ZwitterCo’s manufacturing process lets the company tune the pore size of the zwitterionic membranes, which means the company could expand over time from its current focus on “superfiltration” of particles between 0.001 and 0.01 microns into adjacent markets for “nanofiltration” of smaller particles and “ultrafiltration” of larger particles. The Series A investment will allow the startup to build a 30,000-square-foot pilot production plant in Woburn, Massachusetts, where it will be able to move new polymer formulations to field testing in under one month.
While Rappaport believes zwitterionic membranes will displace most traditional membrane-based filters, there’s an even bigger market in industries where filtration membranes have never been tried. Cleaning up wastewater streams whose waste is currently hauled away or dumped into rivers could make industrial water supplies more predictable, reduce competition for public waters, and help companies sidestep rising municipal water and sewer rates. Tomorrow’s winning climate technologies must reduce costs even as they spare the planet. ZwitterCo’s breakthrough does both.
Jason Pontin is a Partner at DCVC and Chair of ZwitterCo