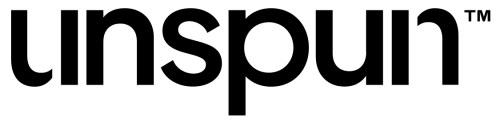

Unspun
Using 3D weaving to reduce the fashion industry’s climate impact
What do your pants have to do with climate change?
A major impediment to a zero-carbon economy is our extreme overconsumption of material goods, including how we make and distribute them — especially the clothes we all wear. Today we’re thrilled to announce that DCVC has led a big Series B investment for Unspun, which is lowering the fashion industry’s shocking levels of overproduction, textile waste, and carbon emissions. The company’s proprietary 3D weaving robots start from yarn to create woven garments, on-demand in onshore microfactories, with far less waste than traditional garment making. We love that Unspun is directly tackling the problem of deadstock, or excess inventory that’s never sold, which translates directly into profound carbon emissions. We endorse the company’s achievable mission to reduce global carbon emissions by a whopping 1%.
We’ve made this investment out of DCVC Climate, our first dedicated climate fund.
Last year the company signed an agreement to build 350 Vega™ machines for Walmart, and it’s ramping up production fast.
The scale of the energy consumption and waste that’s baked into modern clothing production is truly astonishing. McKinsey estimates that the apparel and footwear industries are responsible for as much as 8.6 percent of greenhouse gas emissions. That’s a bigger carbon footprint than aviation (2.5 percent), and it’s on a par with cement (~9 percent). But while we have some great ideas about how to start decarbonizing jet travel and cement plants, the fashion industry suffers from a seemingly intractable set of inefficiencies across the materials, manufacturing, and retail life cycle. Because of long production timelines, brands must order clothes 12 – 18 months in advance. That’s enough time for consumer tastes to change, so there’s a constant mismatch of supply and demand. Historically, that’s led to rampant overproduction and unsold inventory. Of the estimated 100 to 150 billion garments produced annually, 30 percent are never bought by a customer and end up in landfills or incinerators — releasing massive amounts of CO2.
Unspun’s mission will change all that. The company produces a variety of woven garments at its R&D hub in Emeryville, CA, where using its Vega™ machines a pair of pants is woven and assembled in 20 minutes, at least four times faster than traditional methods. It’s a marvel to watch Vega™ in action, spinning faster than the eye can see, simultaneously unspooling thousands of individual yarns and weaving them seamlessly into 3D textiles. The machines feature exquisite textile controls, and they can work with a broad variety of yarns, such as wool, cotton, synthetic fibers, and even twine and recycled plastic. Siting the microfactories in or near the US (or other end-markets) accomplishes four things: creating skilled jobs, meeting consumer demand for locally made garments, decreasing shipping timelines, and shrinking the supply chain emissions profile.
The company designed and debuted a line of wide-leg pants at this past spring’s New York Fashion Week, in partnership with the LA- and NYC-based fashion brand Eckhaus Latta. That’s a canny way to establish the company’s cool factor and position it as an industry leader. But in the end, it’s the future of the planetary climate that we care about, and perhaps the most important feature of the Unspun process is cutting multiple steps out of the traditional garment-making process, significantly shrinking the time between order and delivery. Normally, yarns are woven into fabric in one factory, prepared and finished at another, and cut and sewn at yet another. Then garments flow through a labyrinthine global chain of distributors and warehouses, with delays at every step. By contrast, an onshore Unspun microfactory would leap from yarn to consumer in practically a single step, enabling brands to rapidly produce clothing on-demand and in smaller batches, theoretically driving the industry’s 30 percent overproduction rate to nearly zero.
Unspun’s founders bring the perfect mix of skills to their business. Beth Esponnette, who came up with the idea for the company in 2015, trained in fiber science and apparel design and was a professor of product design at the University of Oregon. Kevin Martin is a mechanical engineer with experience in aerospace, medical devices, and robotics. Walden Lam led Lululemon’s expansion in the Asia-Pacific region and has extensive relationships in the fashion industry. Their potent combination of textile expertise, industry savvy, manufacturing experience, and technical capability is the key to scaling up a hybrid software/hardware business that will help retailers make climate-friendly clothing that consumers want. They’re the kinds of entrepreneurs who make us want to get up every morning, put on our (sustainably produced) pants, and get to work as deep-tech investors.
Milo Werner is a General Parter at DCVC and a Board Member of Unspun. Zachary Bogue is Co-Founder and Managing Partner of DCVC.